Our range of anchors, combined with our exclusive polyester pipeline saddle, provide unparalleled pipeline buoyancy control.
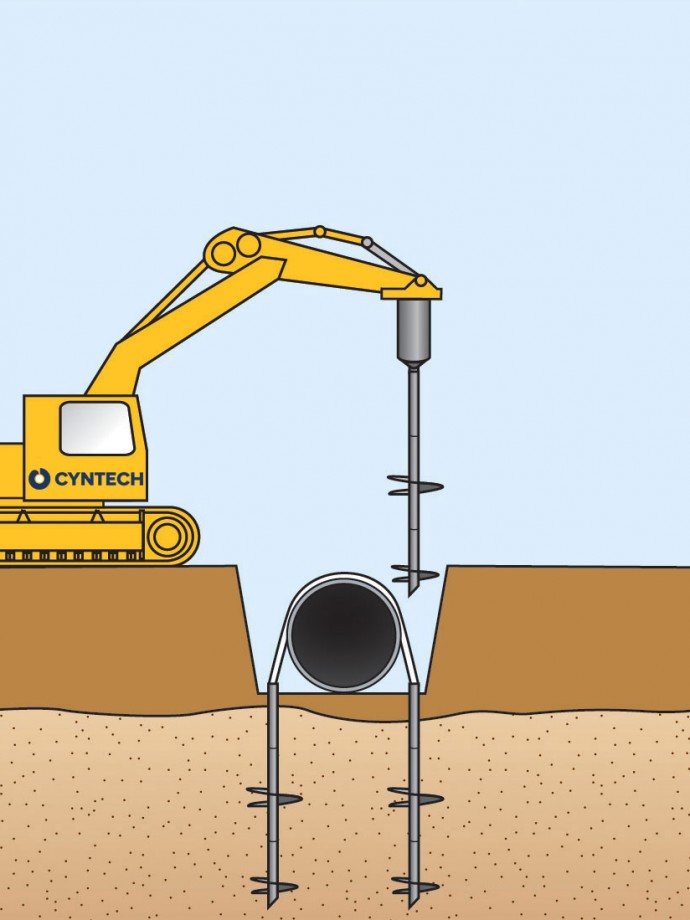
Common uses
Process
We can custom design the optimum anchor system for your specific application, or if required, provide a complete turnkey design and installation service. We offer a range of pipe sizes from 10 to 48 inches.
Our exclusive polyester pipeline saddle provides universal contact with the pipeline while the elasticity of the polyester belt ensures that the load is shared equally between anchor points. There is also no metal-on-metal contact with pipe. These exclusive, non-corroding, low stress polyester pipe saddles, provide unparalleled performance and longevity, regardless of the installation environment.
Our anchor system is designed to provide a hold-down capacity of 2.5 times the buoyant force of the empty pipeline, with typical spacing for an NPS-24 pipeline of 33 meters.
A typical anchor installation crew consist of a five-ton picker truck with a hydraulic drive unit, an operator and two laborers.
Compared to concrete weights, our anchors require less transport and storage space – materials for 10 kilometers of NPS-24 pipeline comprise three truckloads and require just 30 square meters of storage space. Our systems can result in cost savings of up to 80 per cent compared to traditional pipeline buoyancy control methods.
Stress mitigation
The advancement of sophisticated pipeline stress analysis methods has resulted is far greater understanding of why pipelines fail and what can be done to prevent it. Collaborating with the world's premier pipeline engineering firms, Cyntech's designers developed a simple-but-effective method of reducing thermal expansion-induced overbend stresses.
In addition to our standard buoyancy control anchor systems, it is now the standard practice of some of the most well know players in the pipeline industry to utilize our stress mitigation anchor systems, providing permanent protection against excessive stress, upheaval and buckling. Our stress mitigation anchor systems are implemented in much the same way as our standard anchor systems, but are designed to resist greater uplift forces and use specialized saddles to distribute those loads over a greater contact area of pipeline.
Additionally, multiple anchor options are available which allow for anchorage in all types of geotechnical conditions, from extremely weak clays to solid rock.
Cost savings
Our anchor systems can result in cost savings of up to 80 percent compared with traditional pipeline buoyancy control methods.
As our anchors are lightweight and compact, materials, storage and transportation costs, as well as the need for personnel and equipment hours are all reduced significantly. Our exclusive systems also eliminate the need for concrete weights or concrete coated pipe to control pipeline buoyancy.
When comparing the cost of Cyntech Group pipeline anchors versus concrete weight or bag weights, it is important to be accurate.
For example, concrete weights may cost around $550 per weight while an anchor set may cost around $1900 per set. Because of the great capacity and spacing of the anchor set, it is important to calculate the cost of pipeline per meter in addition to the complete supply and install for each method of buoyancy control (including shipping, storage clean-up etc.). This will help determine an accurate number.
Typical concrete weight spacing is five metres while our anchors are spaced at 35 metres. As the chart below shows, there are cost savings to be made. 100 kms of 30-inch pipeline would require 20,000 weight (approx. $11,000,000) versus 1900 anchor sets at a cost of $4,180,000, providing savings of 62 per cent. In this case, weights cost $110 per metre, and our anchors cost as little as $41.80 per metre. The same cost analysis method should be used for bag weights and other weight-type buoyancy systems to compare the true cost of the different buoyancy control methods.
In other words, the larger the pipe diameter, the greater the possibility of increased savings.
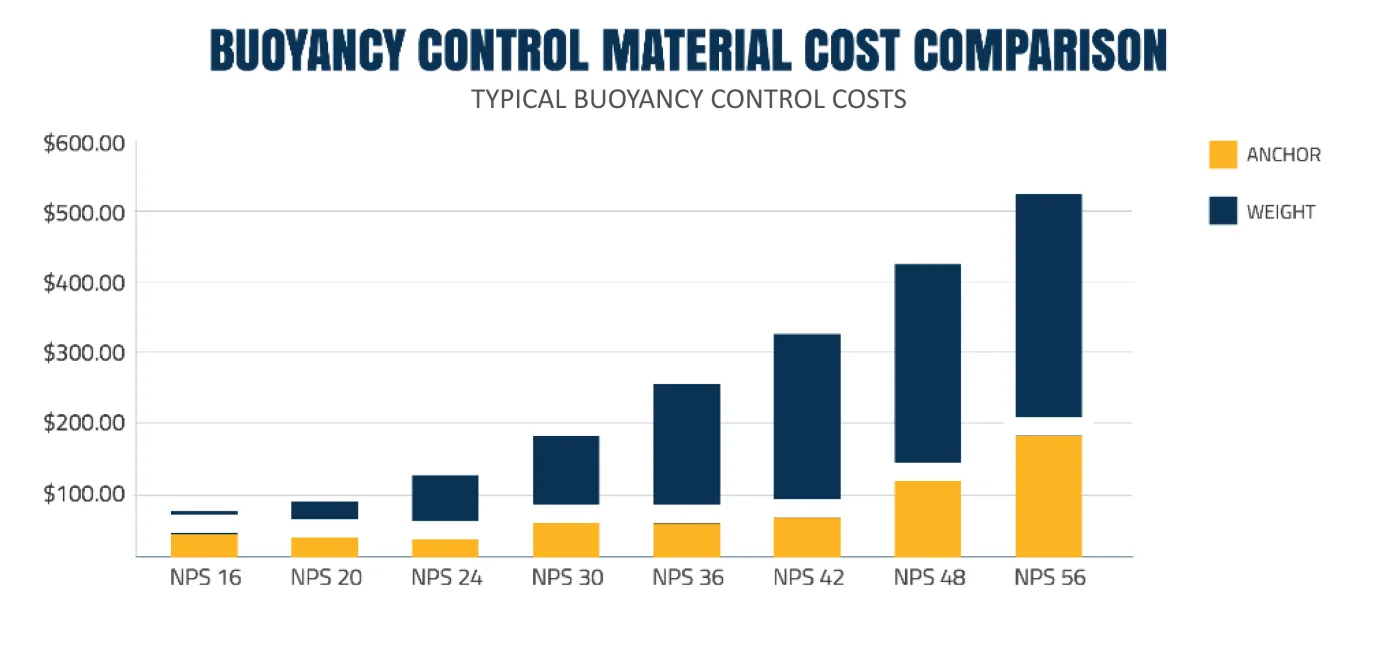