Helical piles (also known as helical piers or screw piles) are constructed using steel shafts with helical flights of various sizes to suit the site-specific ground conditions. Our helical piling systems are a proven deep foundation solution ideal for oil and gas, energy, industrial, rail, and commercial applications. Compared to other types of foundations, helical piles reduce labor, material, equipment, and installation time.
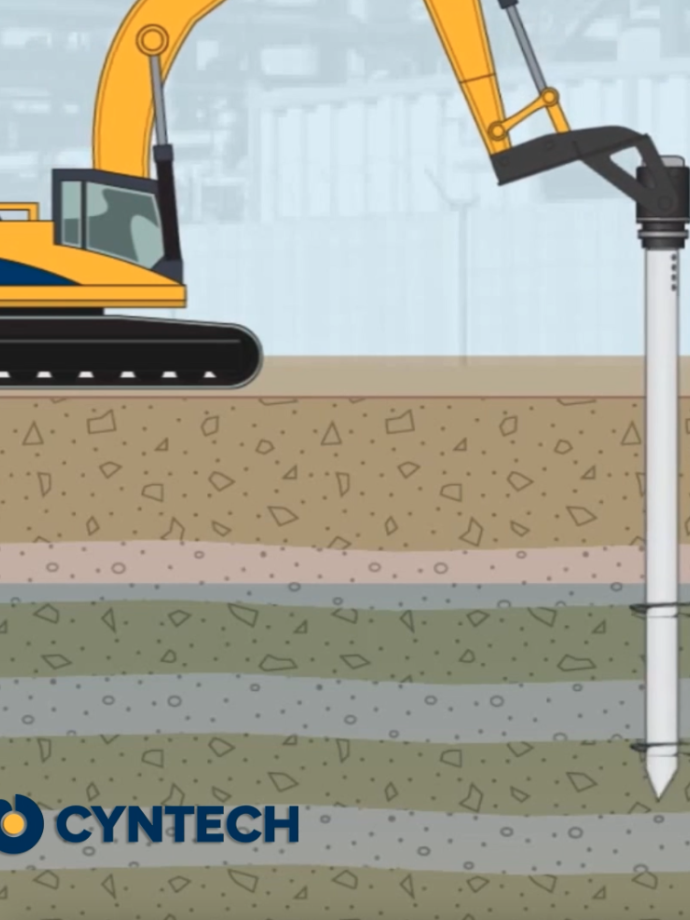
Advantages
Typical applications for our helical pile foundations:
- Structural support (compression or tension) for both permanent and temporary structures
- Replacing any deep foundation where wood, concrete, steel, or auger cast piles are being considered
- Pipe racks, pipe bridges
- Transmission tower foundations and substation foundations
- Rail – Overhead line equipment, stabilization/ground improvement, platforms, etc.
- Skid mounted equipment and buildings
- Building and equipment floor slabs
- Streetlight foundations and highway sign bridges
- Valves and scraper traps, manifolds
- Structures in High-seismic zones
- Underpinning existing foundations
Earthquake performance
If you are operating in an earthquake zone, helical piles may be the solution. They can withstand lateral displacements and tensile forces and offer load resistance and ductile response.
While loss of skin friction is often an issue for other piling options, helical piles are the exception because they are a deep foundation pile with significant end-bearing capacity. Helical piles offer a lower capacity reduction from shaft friction loss during ground liquefaction and all throughout the process and tension capacity loads remain supported by the helix. Once a proper depth is achieved below the liquefaction zone, a helix is placed there to withstand tension loads when a seismic event takes place.
Process
Our engineers will design a custom helical pile foundation for your specific needs using standard soil test data and the loads.
Helical piles are generally installed using standard tracked or wheeled excavators with a torque motor attachment which monitors the torque achieved during installation to ensure predictable pile capacity. The final torque reading is taken over the last 1m of advancement to ensure the pile is achieving the required design capacity before terminating at the correct datum level.
Helical piles are screwed into the soil to the predetermined (design) bearing strata by rotating the steel shafts with the torque motor attached to the excavator plant/rig. They are not driven or vibrated and do not require a hole to be dug or drilled, so the soil around the pile remains undisturbed and no spoils are generated.
Multiple steel sections are connected via a bolted connection and sections are added to achieve the total pile depth.
Individual helical piles can restrain unfactored (SWL) axial loads of up to 2000kN (450 kips) and lateral loads in excess of 250kN (50+ kips), both subject to geotechnical conditions. Significantly higher lateral forces can be resisted by battering the pile, or by incorporating a concrete collar to the upper portion of the pile.
A detailed understanding of the subsurface conditions – especially soil strata type, strata levels and strength (SPT ‘N’ Values) – to depth is necessary to properly interpret the required design and torque capacities.
On completion, the top of the pile can be connected in various ways to the structure by a direct steel flange plate connection or plate/rebar connection to concrete. Torque is monitored during installation to ensure predictable pile capacity, and we can achieve high ultimate capacities safely and economically.
A helical pile can be installed in minutes using standard equipment such as a pole line truck, excavator, or backhoe.
Helical Pile Manufacturing
For all U.S. customers and projects, we manufacture 100% of our helical piles, pile extensions, and pile caps in our Houston (Plantersville), Texas facility whereas our Calgary, Alberta location services the Canadian and overseas markets. Our state-of-the-art workshops include CNC-automated cutting, bending, and welding to produce exact, uniform quality for all parts.
We produce all sizes and configurations of helical piles and pile caps, from 1.5 in (38 mm) and 1.75 in (44 mm) high-strength solid square bar anchors, up to 42 in (1067 mm) diameter round shaft piles.
In total, our facilities share a combined fabrication capacity of 50,000 tons/year with the ability to quickly scale beyond on an as-needed basis. Additionally, we complete upwards of 40,000 feet (12,000 m) of welding production per month. When needed, we can maximize our capacity for output by distributing work among our fabrication shops, enabling our teams to meet your project timelines.
Our quality program was created in full compliance of the ISO 9001:2015 Standard for Quality Assurance, providing continual improvement, consistency of service and product, and complete material traceability.